DAVAO CITY — The development and commercial production of concrete made entirely from fly ash, a residue of coal-fired power plants, is being eyed within the next five years.
“We have a booming construction industry and one of the most widely used materials in the industry is concrete with Portland cement as the main ingredient,” Dr. Michael Angelo B. Promentilla,a professor at De La Salle University’s Chemical Engineering Department, told BusinessWorld in an interview last week on the sidelines of the 2nd ASEAN Science Diplomats Assembly.
Mr. Promentilla, also the head of the Waste and Chemicals Management Unit of the Center for Engineering and Sustainability Development Research, the research arm of the Gokongwei College of Engineering, said the product they are developing is a more environment-friendly construction material.
“The production of cement emits a significant amount of carbon dioxide (CO2). The industry is also energy intensive,” he said
At the same time, using fly ash from the coal-fired energy sector would help manage the power plants’ byproduct.
Mr. Promentilla’s ongoing research project, “Developing Green Cementitious Material for a Carbon-Constrained World,” seeks to use 100% fly ash in making cement to reduce the carbon footprint of the construction material.
The Portland cement currently available in the market already has a 15% fly ash component.
Mr. Promentilla, who refers to his project as “GAMERS” (Geopolymer and Advanced Materials Engineering Research for Sustainability), said “these cement plants emit about two metric tons (MT) of carbon dioxide per year, which is about 5% to 7% of the global anthropogenic CO2 .”
“My project aims to use fly ash alone without using Portland cement. We try to utilize the waste of coal-fired plants to produce material comparable to Portland cement and we call the technology geopolymer,” he explained.
Mr. Promentilla said the project is still in the research and development stage, although they have already successfully created brick out of the geopolymer at the laboratory. They have yet to go on field testing, which means actually using the product to construct a house.
The project has already spent P3 million since it started in 2013, and requires another P10 million for field tests.
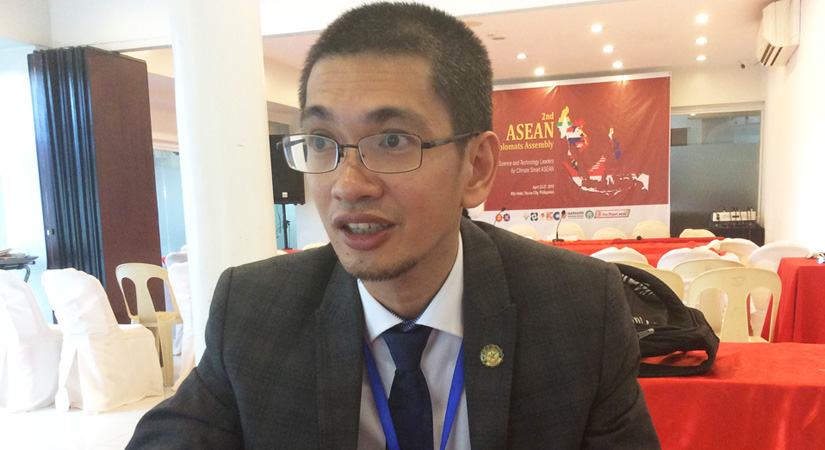
The project has financial support from the ASEAN University Network/Southeast Asia Engineering Education Network (AUN/SEED-Net) — Japan International Cooperation Agency (JICA), and the National Academy of Science and Technology/Department of Science and Technology (NAST/DoST) Grants to Outstanding Achievement in Science and Technology, and collaborators from DLSU Gokongwei College of Engineering, Tokyo Institute of Technology (Japan), and Ho Chi Minh University of Technology (Vietnam).
“R&D usually takes two to three years and with the best scenario, we can come up with a level of technology readiness in five years where we can commercialize it,” he said.
Mr. Promentilla said the geopolymer technology itself is already being used by scientists from France and Australia, but their project is the first in the Philippines and he wants to popularize it as the green and better option.
He said he hopes the construction industry will consider the new technology and “they work with us to produce green materials.”
“I call it upcycling or trying to convert something of low value or something considered waste into a high-value product, which is the framework of a circular economy,” he said.
“We hope we can apply the technology to build houses, low-cost housing or even road embankment,” he added.
Their team is also anticipating other challenges such as establishing standards for the product and introducing legal amendments to make it part of the National Building Code.
In the future, when GAMERS has become mainstream, Mr. Promentilla said he also wants to explore the use of agricultural waste such as abaca fiber, rice hulls or other indigenous materials as a composite to be mixed with geopolymer.
“Utilization of such wastes as sources of reactive alumino-silicate resource is proposed as a viable solution to the pollution problem and at the same time as an economical option in the design of sustainable construction materials for a carbon-constrained world,” he said.
Link: https://www.bworldonline.com/project-seeks-to-use-100-fly-ash-to-make-cement/